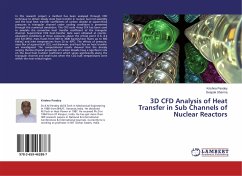
3D CFD Analysis of Heat Transfer in Sub Channels of Nuclear Reactors
Versandkostenfrei!
Versandfertig in 6-10 Tagen
36,99 €
inkl. MwSt.
PAYBACK Punkte
18 °P sammeln!
In this research project a method has been analysed through CFD technique to obtain steady state heat transfer in nuclear fuel rod assembly and the local heat transfer coefficients of carbon dioxide at supercritical pressures in triangular channel under cooling conditions is presented through the numerical simulation. The CFD code Ansys CFX has been used to simulate the convective heat transfer coefficient of the triangular channel. Supercritical CO2 heat-transfer data were obtained at reactor-equivalent conditions at three pressures above the critical point (7.6, 8.4 and 8.8 MPa), mass fluxes...
In this research project a method has been analysed through CFD technique to obtain steady state heat transfer in nuclear fuel rod assembly and the local heat transfer coefficients of carbon dioxide at supercritical pressures in triangular channel under cooling conditions is presented through the numerical simulation. The CFD code Ansys CFX has been used to simulate the convective heat transfer coefficient of the triangular channel. Supercritical CO2 heat-transfer data were obtained at reactor-equivalent conditions at three pressures above the critical point (7.6, 8.4 and 8.8 MPa), mass fluxes from 840 to 3000 kg/m2s,heat fluxes up to 600 kW/m2 and inlet temperatures from 20 to 40ºC. The effects of pressure, mass flux of supercritical CO2, rod diameter, and heat flux on heat transfer are investigated. The computational results showed that the sharply varying thermo physical properties of carbon dioxide have a significant role on the local heat transfer coefficient which varies significantly along the triangular channel and small tube when the CO2 bulk temperatures were within the near-critical region.