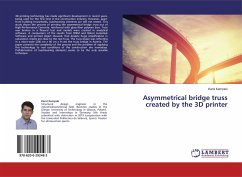
Asymmetrical bridge truss created by the 3D printer
Versandkostenfrei!
Versandfertig in 6-10 Tagen
26,99 €
inkl. MwSt.
PAYBACK Punkte
13 °P sammeln!
3D printing technology has made significant development in recent years, being used for the first time in the construction industry. However, apart from building households, load-bearing elements are still not tested. This study shows the process of printing the asymmetrical bridge truss out of High-Performance Concrete, reinforced with glass fiber polymer bars. Truss was broken in a flexural test and models were created in analytical software. A comparison of the results from RFEM and Robot Autodesk Software and printed object showed, that despite huge simplification in calculation results ar...
3D printing technology has made significant development in recent years, being used for the first time in the construction industry. However, apart from building households, load-bearing elements are still not tested. This study shows the process of printing the asymmetrical bridge truss out of High-Performance Concrete, reinforced with glass fiber polymer bars. Truss was broken in a flexural test and models were created in analytical software. A comparison of the results from RFEM and Robot Autodesk Software and printed object showed, that despite huge simplification in calculation results are close to the real truss. The truss shape was reflecting in a micro-scale (200 cm x 40 cm x 9 cm) the truss bridge in Austria. The paper presents the complexity of the process and the problem of applying this technology to real conditions of the construction site nowadays. Prefabrication of load-bearing elements seems to be the only sensible technique.