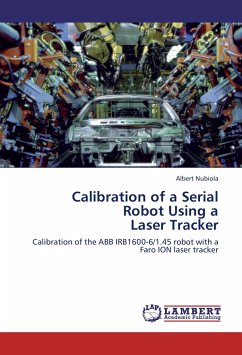
Calibration of a Serial Robot Using a Laser Tracker
Calibration of the ABB IRB1600-6/1.45 robot with a Faro ION laser tracker
Versandkostenfrei!
Versandfertig in 6-10 Tagen
38,99 €
inkl. MwSt.
PAYBACK Punkte
19 °P sammeln!
The positioning performance of the industrial robot ABB IRB 1600-6/1.45 is deeply studied with a Faro ION laser tracker. Axes 2, 3 and 6 are found to have a non-geometrical behaviour. Different robot models are taken into account for calibration. The level-3 model takes into account the geometrical defaults as well as four error parameters related to stiffness in axes 2 and 3, plus four other error parameters used to fit a second-order Fourier series to the non-linearity of axis 6. The Nelder-Mead technique is used to find the error parameters of the model. The ISO 9283 tests are found to be n...
The positioning performance of the industrial robot ABB IRB 1600-6/1.45 is deeply studied with a Faro ION laser tracker. Axes 2, 3 and 6 are found to have a non-geometrical behaviour. Different robot models are taken into account for calibration. The level-3 model takes into account the geometrical defaults as well as four error parameters related to stiffness in axes 2 and 3, plus four other error parameters used to fit a second-order Fourier series to the non-linearity of axis 6. The Nelder-Mead technique is used to find the error parameters of the model. The ISO 9283 tests are found to be not complete enough to validate the position performance of the robot. An extensive validation procedure is applied in addition to the ISO 9283 tests. Several tests are also applied to the Faro laser tracker to validate its precision, repeatability and stability. Repeatability tests and stabilization tests are also performed to the calibrated robot. Finally, circular tests are applied with a Renishaw QC20-W telescopic bar to validate the improvement of the robot's accuracy.