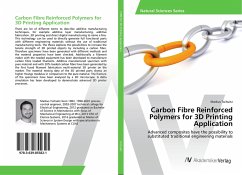
Carbon Fibre Reinforced Polymers for 3D Printing Application
Advanced composites have the possibility to substituted traditional engineering materials
Versandkostenfrei!
Versandfertig in 6-10 Tagen
22,99 €
inkl. MwSt.
PAYBACK Punkte
11 °P sammeln!
There are lot of different terms to describe additive manufacturing techniques, for example additive layer manufacturing, additive fabrication, 3D printing and direct digital manufacturing to name a few. This technology can be used to directly generate full functional parts with different engineering materials without the use of traditional manufacturing tools. The thesis explores the possibilities to increase the tensile strength of 3D printed objects by including a carbon fibre. Therefore specimens have been generated with different methods and the material properties have been checked. Addi...
There are lot of different terms to describe additive manufacturing techniques, for example additive layer manufacturing, additive fabrication, 3D printing and direct digital manufacturing to name a few. This technology can be used to directly generate full functional parts with different engineering materials without the use of traditional manufacturing tools. The thesis explores the possibilities to increase the tensile strength of 3D printed objects by including a carbon fibre. Therefore specimens have been generated with different methods and the material properties have been checked. Additionally a filament maker with the needed equipment has been developed to manufacture carbon fibre loaded filaments. Additive manufactured specimen with pure material and with 20% loaded carbon fibre have been generated by the first fused filament fabrication multi-material 3D printer on the market. The material testing data of the 3D printed parts shows an higher Youngs modulus in comparison to the pure material. The fracture of the specimens have been analysed by a 3D microscope. A delta simulation has been developed to demonstrate advanced 3D printer processes.