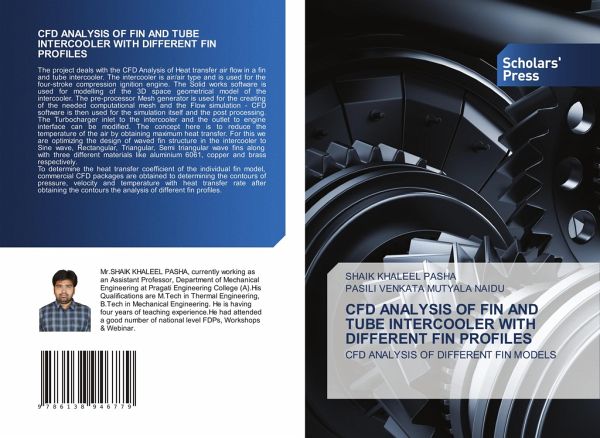
CFD ANALYSIS OF FIN AND TUBE INTERCOOLER WITH DIFFERENT FIN PROFILES
CFD ANALYSIS OF DIFFERENT FIN MODELS
Versandkostenfrei!
Versandfertig in 6-10 Tagen
30,99 €
inkl. MwSt.
PAYBACK Punkte
15 °P sammeln!
The project deals with the CFD Analysis of Heat transfer air flow in a fin and tube intercooler. The intercooler is air/air type and is used for the four-stroke compression ignition engine. The Solid works software is used for modelling of the 3D space geometrical model of the intercooler. The pre-processor Mesh generator is used for the creating of the needed computational mesh and the Flow simulation - CFD software is then used for the simulation itself and the post processing. The Turbocharger inlet to the intercooler and the outlet to engine interface can be modified. The concept here is t...
The project deals with the CFD Analysis of Heat transfer air flow in a fin and tube intercooler. The intercooler is air/air type and is used for the four-stroke compression ignition engine. The Solid works software is used for modelling of the 3D space geometrical model of the intercooler. The pre-processor Mesh generator is used for the creating of the needed computational mesh and the Flow simulation - CFD software is then used for the simulation itself and the post processing. The Turbocharger inlet to the intercooler and the outlet to engine interface can be modified. The concept here is to reduce the temperature of the air by obtaining maximum heat transfer. For this we are optimizing the design of waved fin structure in the intercooler to Sine wave, Rectangular, Triangular, Semi triangular wave fins along with three different materials like aluminium 6061, copper and brass respectively.To determine the heat transfer coefficient of the individual fin model, commercial CFD packages are obtained to determining the contours of pressure, velocity and temperature with heat transfer rate after obtaining the contours the analysis of different fin profiles.