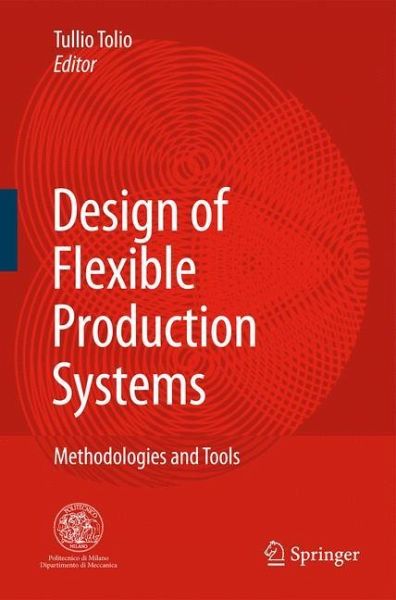
Design of Flexible Production Systems
Methodologies and Tools
Herausgegeben: Tolio, Tullio
Versandkostenfrei!
Versandfertig in 6-10 Tagen
127,99 €
inkl. MwSt.
PAYBACK Punkte
64 °P sammeln!
In the last decade, the production of mechanical components to be assembled in final products produced in high volumes (e.g. cars, mopeds, industrial vehicles, etc.) has undergone deep changes due to the overall modifications in the way companies compete. Companies must consider competitive factors such as short lead times, tight product tolerances, frequent market changes and cost reduction. Anyway, companies often have to define production objectives as trade-offs among these critical factors since it can be difficult to improve all of them.
Even if system flexibility is often considered a fundamental requirement for firms, it is not always a desirable characteristic of a system because it requires relevant investment cost which can jeopardize the profitability of the firm. Dedicated systems are not able to adapt to changes of the product characteristics while flexible systems offer more flexibility than what is needed, thus increasing investment and operative costs. Production contexts characterized by mid to high demand volume of well identified families of products in continuous evolution do not require the highest level of flexibility; therefore, manufacturing system flexibility must be rationalized and it is necessary to find out the best trade-off between productivity and flexibility by designing manufacturing systems endowed with the right level of flexibility required by the production problem. This new class of production systems can be named Focused Flexibility Manufacturing Systems-FFMSs.
The flexibility degree in FFMSs is related to their ability to cope with volume, mix and technological changes, and it must take into account both present and future changes. The required level of system flexibility impacts on the architecture of the system and the explicit design of flexibility often leads to hybrid systems, i.e. automated integrated systems in which parts can be processed by both general purpose and dedicated machines. This is a key issue of FFMSs and results from the matching of flexibility and productivity that respectively characterize FMSs and Dedicated Manufacturing Systems (DMSs).
The market share of the EU in the machine tool sector is 44%; the introduction of focused flexibility would be particularly important for machine tool builders whose competitive advantage is based on the ability of customizing their systems on the basis of needs of their customers. In fact, even if current production contexts frequently present situations which would fit well with the FFMS approach, tradition and know-how of machine tool builders play a crucial role. Firms often agree with the focused flexibility vision, nevertheless they decide not to pay the risk and efforts related to the design of this new system architecture. This is due also to the lack of well-structured design approaches which can help machine tool builders to configure innovative systems. Therefore, the FFMS topic is studied through the book chapters following a shared mission: "To define methodologies and tools to design production systems with a minimum level of flexibility needed to face, during their lifecycle, the product and process evolution both in the technological and demand aspects. The goal is to find out the optimal trade-off between flexibility and productivity".
The book framework follows the architecture which has been developed to address the FFMS Design problem. This architecture is both broad and detailed, since it pays attention to all the relevant levels in a firm hierarchy which are involved in the system design. Moreover, the architecture is innovative because it models both the point of view of the machine tool builder and the point of view of the system user.
The architecture starts analyzing Manufacturing Strategy issues and generating the possible demand scenario to be faced. Technological aspects play a key role while solving process plan problems for the products in the part family. Strategic and technological data becomes input when a machine tool builder performs system configuration. The resulting system configurations are possible solutions that a system user considers when planning its system capacity.
All the steps of the architecture are deeply studied, developing methods and tools to address each subproblem. Particular attention is paid to the methodologies adopted to face the different subproblems: mathematical programming, stochastic programming, simulation techniques and inverse kinematics have been used.
The whole architecture provides a general approach to implement the right degree of flexibility and it allows to study how different aspects and decisions taken in a firm impact on each other. The work presented in the book is innovative because it gives links among different research fields, such as Manufacturing Strategy, Process Plan, System Design, Capacity Planning and Performance Evaluation; moreover, it helps to formalize and rationalize a critical area such as manufacturing system flexibility.
The addressed problem is relevant at an academic level but, also, at an industrial level. A great deal of industrial sectors need to address the problem of designing systems with the right degree of flexibility; for instance, automotive, white goods, electrical and electronic goods industries, etc.
Attention to industrial issues is confirmed by empirical studies and real case analyses which are presented within the book chapters.
Even if system flexibility is often considered a fundamental requirement for firms, it is not always a desirable characteristic of a system because it requires relevant investment cost which can jeopardize the profitability of the firm. Dedicated systems are not able to adapt to changes of the product characteristics while flexible systems offer more flexibility than what is needed, thus increasing investment and operative costs. Production contexts characterized by mid to high demand volume of well identified families of products in continuous evolution do not require the highest level of flexibility; therefore, manufacturing system flexibility must be rationalized and it is necessary to find out the best trade-off between productivity and flexibility by designing manufacturing systems endowed with the right level of flexibility required by the production problem. This new class of production systems can be named Focused Flexibility Manufacturing Systems-FFMSs.
The flexibility degree in FFMSs is related to their ability to cope with volume, mix and technological changes, and it must take into account both present and future changes. The required level of system flexibility impacts on the architecture of the system and the explicit design of flexibility often leads to hybrid systems, i.e. automated integrated systems in which parts can be processed by both general purpose and dedicated machines. This is a key issue of FFMSs and results from the matching of flexibility and productivity that respectively characterize FMSs and Dedicated Manufacturing Systems (DMSs).
The market share of the EU in the machine tool sector is 44%; the introduction of focused flexibility would be particularly important for machine tool builders whose competitive advantage is based on the ability of customizing their systems on the basis of needs of their customers. In fact, even if current production contexts frequently present situations which would fit well with the FFMS approach, tradition and know-how of machine tool builders play a crucial role. Firms often agree with the focused flexibility vision, nevertheless they decide not to pay the risk and efforts related to the design of this new system architecture. This is due also to the lack of well-structured design approaches which can help machine tool builders to configure innovative systems. Therefore, the FFMS topic is studied through the book chapters following a shared mission: "To define methodologies and tools to design production systems with a minimum level of flexibility needed to face, during their lifecycle, the product and process evolution both in the technological and demand aspects. The goal is to find out the optimal trade-off between flexibility and productivity".
The book framework follows the architecture which has been developed to address the FFMS Design problem. This architecture is both broad and detailed, since it pays attention to all the relevant levels in a firm hierarchy which are involved in the system design. Moreover, the architecture is innovative because it models both the point of view of the machine tool builder and the point of view of the system user.
The architecture starts analyzing Manufacturing Strategy issues and generating the possible demand scenario to be faced. Technological aspects play a key role while solving process plan problems for the products in the part family. Strategic and technological data becomes input when a machine tool builder performs system configuration. The resulting system configurations are possible solutions that a system user considers when planning its system capacity.
All the steps of the architecture are deeply studied, developing methods and tools to address each subproblem. Particular attention is paid to the methodologies adopted to face the different subproblems: mathematical programming, stochastic programming, simulation techniques and inverse kinematics have been used.
The whole architecture provides a general approach to implement the right degree of flexibility and it allows to study how different aspects and decisions taken in a firm impact on each other. The work presented in the book is innovative because it gives links among different research fields, such as Manufacturing Strategy, Process Plan, System Design, Capacity Planning and Performance Evaluation; moreover, it helps to formalize and rationalize a critical area such as manufacturing system flexibility.
The addressed problem is relevant at an academic level but, also, at an industrial level. A great deal of industrial sectors need to address the problem of designing systems with the right degree of flexibility; for instance, automotive, white goods, electrical and electronic goods industries, etc.
Attention to industrial issues is confirmed by empirical studies and real case analyses which are presented within the book chapters.
In the last decade, the production of mechanical components to be assembled in final products produced in high volumes (e.g. cars, mopeds, industrial vehicles, etc.) has undergone deep changes due to the overall modifications in the way companies compete. Companies must consider competitive factors such as short lead times, tight product tolerances, frequent market changes and cost reduction. Anyway, companies often have to define production objectives as trade-offs among these critical factors since it can be difficult to improve all of them.
Even if system flexibility is often considered a fundamental requirement for firms, it is not always a desirable characteristic of a system because it requires relevant investment cost which can jeopardize the profitability of the firm. Dedicated systems are not able to adapt to changes of the product characteristics while flexible systems offer more flexibility than what is needed, thus increasing investment and operative costs.Production contexts characterized by mid to high demand volume of well identified families of products in continuous evolution do not require the highest level of flexibility; therefore, manufacturing system flexibility must be rationalized and it is necessary to find out the best trade-off between productivity and flexibility by designing manufacturing systems endowed with the right level of flexibility required by the production problem. This new class of production systems can be named Focused Flexibility Manufacturing Systems-FFMSs.
The flexibility degree in FFMSs is related to their ability to cope with volume, mix and technological changes, and it must take into account both present and future changes. The required level of system flexibility impacts on the architecture of the system and the explicit design of flexibility often leads to hybrid systems, i.e. automated integrated systems in which parts can be processed by both general purpose and dedicated machines. This is a key issue of FFMSs and results from the matching of flexibility and productivity that respectively characterize FMSs and Dedicated Manufacturing Systems (DMSs).
The market share of the EU in the machine tool sector is 44%; the introduction of focused flexibility would be particularly important for machine tool builders whose competitive advantage is based on the ability of customizing their systems on the basis of needs of their customers. In fact, even if current production contexts frequently present situations which would fit well with the FFMS approach, tradition and know-how of machine tool builders play a crucial role. Firms often agree with the focused flexibility vision, nevertheless they decide not to pay the risk and efforts related to the design of this new system architecture. This is due also to the lack of well-structured design approaches which can help machine tool builders to configure innovative systems. Therefore, the FFMS topic is studied through the book chapters following a shared mission: "To define methodologies and tools to design production systems with a minimum level of flexibility needed to face, during their lifecycle, the product and process evolution both in the technological and demand aspects. The goal is to find out the optimal trade-off between flexibility and productivity".
The book framework follows the architecture which has been developed to address the FFMS Design problem. This architecture is both broad and detailed, since it pays attention to all the relevant levels in a firm hierarchy which are involved in the system design. Moreover, the architecture is innovative because it models both the point of view of the machine tool builder and the point of view of the system user.
The architecture starts analyzing Manufacturing Strategy issues and generating the possible demand scenario to be faced. Technological aspects play a key role while solving process plan problems for the products in the part family. St
Even if system flexibility is often considered a fundamental requirement for firms, it is not always a desirable characteristic of a system because it requires relevant investment cost which can jeopardize the profitability of the firm. Dedicated systems are not able to adapt to changes of the product characteristics while flexible systems offer more flexibility than what is needed, thus increasing investment and operative costs.Production contexts characterized by mid to high demand volume of well identified families of products in continuous evolution do not require the highest level of flexibility; therefore, manufacturing system flexibility must be rationalized and it is necessary to find out the best trade-off between productivity and flexibility by designing manufacturing systems endowed with the right level of flexibility required by the production problem. This new class of production systems can be named Focused Flexibility Manufacturing Systems-FFMSs.
The flexibility degree in FFMSs is related to their ability to cope with volume, mix and technological changes, and it must take into account both present and future changes. The required level of system flexibility impacts on the architecture of the system and the explicit design of flexibility often leads to hybrid systems, i.e. automated integrated systems in which parts can be processed by both general purpose and dedicated machines. This is a key issue of FFMSs and results from the matching of flexibility and productivity that respectively characterize FMSs and Dedicated Manufacturing Systems (DMSs).
The market share of the EU in the machine tool sector is 44%; the introduction of focused flexibility would be particularly important for machine tool builders whose competitive advantage is based on the ability of customizing their systems on the basis of needs of their customers. In fact, even if current production contexts frequently present situations which would fit well with the FFMS approach, tradition and know-how of machine tool builders play a crucial role. Firms often agree with the focused flexibility vision, nevertheless they decide not to pay the risk and efforts related to the design of this new system architecture. This is due also to the lack of well-structured design approaches which can help machine tool builders to configure innovative systems. Therefore, the FFMS topic is studied through the book chapters following a shared mission: "To define methodologies and tools to design production systems with a minimum level of flexibility needed to face, during their lifecycle, the product and process evolution both in the technological and demand aspects. The goal is to find out the optimal trade-off between flexibility and productivity".
The book framework follows the architecture which has been developed to address the FFMS Design problem. This architecture is both broad and detailed, since it pays attention to all the relevant levels in a firm hierarchy which are involved in the system design. Moreover, the architecture is innovative because it models both the point of view of the machine tool builder and the point of view of the system user.
The architecture starts analyzing Manufacturing Strategy issues and generating the possible demand scenario to be faced. Technological aspects play a key role while solving process plan problems for the products in the part family. St