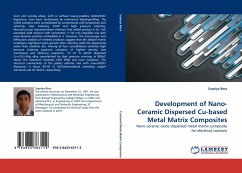
Development of Nano-Ceramic Dispersed Cu-based Metal Matrix Composites
Nano ceramic oxide dispersed metal matrix composite for electrical contacts
Versandkostenfrei!
Versandfertig in 6-10 Tagen
44,99 €
inkl. MwSt.
PAYBACK Punkte
22 °P sammeln!
CuCr and CuCrAg alloys, with or without nanocrystalline Al2O3/ZrO2 dispersion, have been synthesized by mechanical alloying/milling. The milled powders were consolidated by conventional cold compaction and sintering, laser sintering, ECAP and high pressure sintering. Microstructural characterization evidence that milled product is Cu- rich extended solid solution with nanometric (< 50 nm) crystallite size with nano-alumina particles embedded in it. However, the microscopic and diffraction analysis of sintered products suggest that the alloyed matrix undergoes significant grain growth after sin...
CuCr and CuCrAg alloys, with or without nanocrystalline Al2O3/ZrO2 dispersion, have been synthesized by mechanical alloying/milling. The milled powders were consolidated by conventional cold compaction and sintering, laser sintering, ECAP and high pressure sintering. Microstructural characterization evidence that milled product is Cu- rich extended solid solution with nanometric (< 50 nm) crystallite size with nano-alumina particles embedded in it. However, the microscopic and diffraction analysis of sintered products suggest that the alloyed matrix undergoes significant grain growth after sintering while the dispersoids retain their ultrafine size. Among all four consolidation methods high pressure sintering produces compacts of highest density, and mechanical and electrical properties. 10 wt % Al2O3 dispersed Cu-4.5Cr-3Ag alloy consolidated by high pressure sintering at 800oC shows the maximum hardness (435 VHN) and wear resistance. The electrical conductivity of the pellets without and with nano-Al2O3 dispersion is about 40-45 % IACS(international annealing copper standard) and 35 %IACS, respectively.