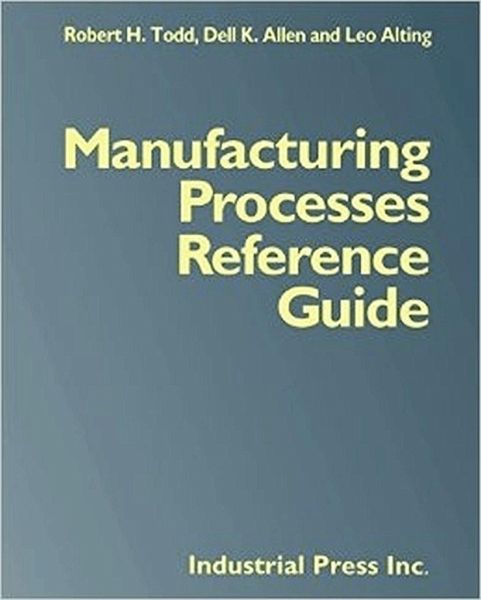
Manufacturing Processes Reference Guide
Versandkostenfrei!
Versandfertig in über 4 Wochen
85,99 €
inkl. MwSt.
PAYBACK Punkte
43 °P sammeln!
Breaks down the treatment of each process into three categories: Knowledge, Application, and Development and organizes each process family based on common characteristics. Comprehensively illustrates, defines, and explains each process to provide the reader with an unequaled understanding of the process and its applications. Encourages an appreciation of the integration of design and manufacturing engineering activities that results in more practical, less expensive, and better designed products for the consumer.