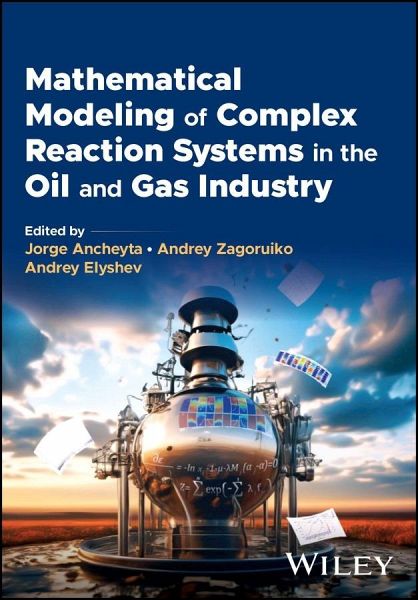
Mathematical Modeling of Complex Reaction Systems in the Oil and Gas Industry
Versandkostenfrei!
Versandfertig in 2-4 Wochen
134,99 €
inkl. MwSt.
PAYBACK Punkte
67 °P sammeln!
Master the fundamentals of reaction systems modeling for the age of decarbonization Reactor design is one of the most important parts of the oil and gas industry, with reactor processes and the accompanying technologies constantly evolving to meet industry needs. A crucial component of effective reactor design is modelling complex reaction systems, which can help predict commercial performance, shape safety procedures, and more. At a time when decarbonization and clean energy transition are among the fundamental global technological challenges, it has never been more important for engineers to...
Master the fundamentals of reaction systems modeling for the age of decarbonization Reactor design is one of the most important parts of the oil and gas industry, with reactor processes and the accompanying technologies constantly evolving to meet industry needs. A crucial component of effective reactor design is modelling complex reaction systems, which can help predict commercial performance, shape safety procedures, and more. At a time when decarbonization and clean energy transition are among the fundamental global technological challenges, it has never been more important for engineers to grasp the cutting edge of reaction system modelling. Mathematical Modeling of Complex Reaction Systems in the Oil and Gas Industry provides a systematic introduction to this timely subject. Each chapter provides a step-by-step description of the kinetic and reactor models for a particular kind of process and its accompanying systems. Backed by voluminous experimental data and incorporating extensive simulation results, the book constitutes an indispensable contribution to the global search for clean energy solutions. Mathematical Modeling of Complex Reaction Systems in the Oil and Gas Industry readers will also find: * All the required tools for developing new reactor models for different reaction scales * Detailed discussion of topics including hydrocracking of heavy oils, catalyst deactivation, oxidative regeneration of catalysts, and many more * Extensive treatment of both steady-state and dynamic simulations Mathematical Modeling of Complex Reaction Systems in the Oil and Gas Industry is ideal for chemical and process engineers, computational chemists and modelers, catalysis researchers, and any other researchers or professionals in petrochemical engineering and the oil and gas industry.