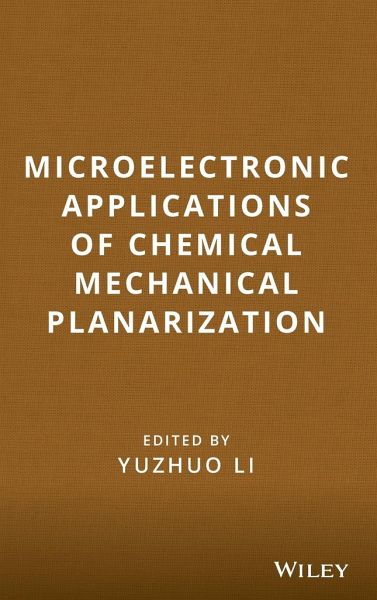
Microelectronic Applications of Chemical Mechanical Planarization
PAYBACK Punkte
93 °P sammeln!
Microelectronic Applications Using Chemical Mechanical Planarization provides a systematic and comprehensive description of current CMP technology used in high-tech products such as video games, portable communications devices, and high-speed computers. It covers includes new designs, capabilities, and emerging technologies, including topics like CMP with nanomaterials and technologies like MEMS (Micro-Electro-Mechanical Systems). It also covers fundamentals and basic science, making it an ideal introduction for CMP newcomers and a valuable reference for professionals.
An authoritative, systematic, and comprehensive description of current CMP technology
Chemical Mechanical Planarization (CMP) provides the greatest degree of planarization of any known technique. The current standard for integrated circuit (IC) planarization, CMP is playing an increasingly important role in other related applications such as microelectromechanical systems (MEMS) and computer hard drive manufacturing. This reference focuses on the chemical aspects of the technology and includes contributions from the foremost experts on specific applications. After a detailed overview of the fundamentals and basic science of CMP, Microelectronic Applications of Chemical Mechanical Planarization:
_
Provides in-depth coverage of a wide range of state-of-the-art technologies and applications
_
Presents information on new designs, capabilities, and emerging technologies, including topics like CMP with nanomaterials and 3D chips
_
Discusses different types of CMP tools, pads for IC CMP, modeling, and the applicability of tribometrology to various aspects of CMP
_
Covers nanotopography, CMP performance and defect profiles, CMP waste treatment, and the chemistry and colloidal properties of the slurries used in CMP
_
Provides a perspective on the opportunities and challenges of the next fifteen years
Complete with case studies, this is a valuable, hands-on resource for professionals, including process engineers, equipment engineers, formulation chemists, IC manufacturers, and others. With systematic organization and questions at the end of each chapter to facilitate learning, it is an ideal introduction to CMP and an excellent text for students in advanced graduate courses that cover CMP or related semiconductor manufacturing processes.
Chemical Mechanical Planarization (CMP) provides the greatest degree of planarization of any known technique. The current standard for integrated circuit (IC) planarization, CMP is playing an increasingly important role in other related applications such as microelectromechanical systems (MEMS) and computer hard drive manufacturing. This reference focuses on the chemical aspects of the technology and includes contributions from the foremost experts on specific applications. After a detailed overview of the fundamentals and basic science of CMP, Microelectronic Applications of Chemical Mechanical Planarization:
_
Provides in-depth coverage of a wide range of state-of-the-art technologies and applications
_
Presents information on new designs, capabilities, and emerging technologies, including topics like CMP with nanomaterials and 3D chips
_
Discusses different types of CMP tools, pads for IC CMP, modeling, and the applicability of tribometrology to various aspects of CMP
_
Covers nanotopography, CMP performance and defect profiles, CMP waste treatment, and the chemistry and colloidal properties of the slurries used in CMP
_
Provides a perspective on the opportunities and challenges of the next fifteen years
Complete with case studies, this is a valuable, hands-on resource for professionals, including process engineers, equipment engineers, formulation chemists, IC manufacturers, and others. With systematic organization and questions at the end of each chapter to facilitate learning, it is an ideal introduction to CMP and an excellent text for students in advanced graduate courses that cover CMP or related semiconductor manufacturing processes.
Dieser Artikel kann nur an eine deutsche Lieferadresse ausgeliefert werden.