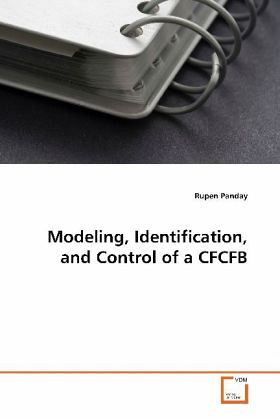
Modeling, Identification, and Control of a CFCFB
Versandkostenfrei!
Versandfertig in 6-10 Tagen
32,99 €
inkl. MwSt.
PAYBACK Punkte
16 °P sammeln!
Circulating fluidized bed (CFB) is used extensively in petrochemical industries especially for fluid catalytic cracking, coal combustion or gasification and various other chemical processes. New 2-region measurement model describing the bed height in the standpipe of a cold model present at National Energy Technology Laboratory (NETL), US Department of Energy, Morgantown, WV, is formulated. On the other hand, system identification of a NETL cold flow circulating fluidized bed (CFCFB) is carried out using a nonlinear model under multiple model identification approach to predict solids circulati...
Circulating fluidized bed (CFB) is used extensively
in petrochemical industries especially for fluid
catalytic cracking, coal combustion or gasification
and various other chemical processes. New 2-region
measurement model describing the bed height in the
standpipe of a cold model present at National Energy
Technology Laboratory (NETL), US Department of
Energy, Morgantown, WV, is formulated. On the other
hand, system identification of a NETL cold flow
circulating fluidized bed (CFCFB) is carried out
using a nonlinear model under multiple model
identification approach to predict solids
circulation rate (SCR) in a wide operating range.
However, the CFCFB was approximated by a linear
model when it was believed to operate linearly in a
single operating regime. A real time pressure drop
model based on the Recursive Prediction Error Method
(RPEM) is built to predict the split of move air
flow between the standpipe and L-valve, and to
determine routes of additional aerations fed to the
standpipe. Finally, the optimal control of SCR
affecting the heat and mass transfer characteristics
which in turn impacts the efficiency of various
chemical processes is carried out.
in petrochemical industries especially for fluid
catalytic cracking, coal combustion or gasification
and various other chemical processes. New 2-region
measurement model describing the bed height in the
standpipe of a cold model present at National Energy
Technology Laboratory (NETL), US Department of
Energy, Morgantown, WV, is formulated. On the other
hand, system identification of a NETL cold flow
circulating fluidized bed (CFCFB) is carried out
using a nonlinear model under multiple model
identification approach to predict solids
circulation rate (SCR) in a wide operating range.
However, the CFCFB was approximated by a linear
model when it was believed to operate linearly in a
single operating regime. A real time pressure drop
model based on the Recursive Prediction Error Method
(RPEM) is built to predict the split of move air
flow between the standpipe and L-valve, and to
determine routes of additional aerations fed to the
standpipe. Finally, the optimal control of SCR
affecting the heat and mass transfer characteristics
which in turn impacts the efficiency of various
chemical processes is carried out.