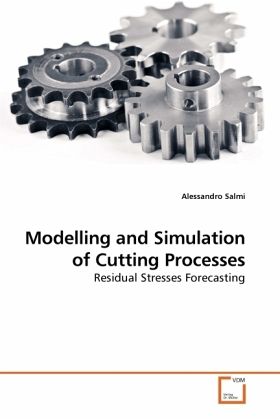
Modelling and Simulation of Cutting Processes
Residual Stresses Forecasting
Versandkostenfrei!
Versandfertig in 6-10 Tagen
38,99 €
inkl. MwSt.
PAYBACK Punkte
19 °P sammeln!
Machining induced residual stress has been a research topic since the middle of the twentieth century. Experimental findings, analytical modelling, finite element modelling and various combinations of those have been proposed. Currently, computational models have great value in increasing the understanding of the cutting process and in reducing the number of experiments which traditionally are used for tool design, process selection, machinability evaluation, and virtual manufacturing. This work proposes a coherent and accurate study of the industrial process of machining pointing out the diff...
Machining induced residual stress has been a research topic since the middle of the twentieth century. Experimental findings, analytical modelling, finite element modelling and various combinations of those have been proposed. Currently, computational models have great value in increasing the understanding of the cutting process and in reducing the number of experiments which traditionally are used for tool design, process selection, machinability evaluation, and virtual manufacturing. This work proposes a coherent and accurate study of the industrial process of machining pointing out the difficulties when considering a finite element model. An extensive work has been carried out comparing the numerical results which can be achieved using different numerical tools with the experimental evidence. A sensitivity analysis on both material modelling and process parameters has been carried out to point out the actual limitations of the available numerical tools for this kind of industrial process simulations. The focus is on the residual stresses prediction as a final output of the simulation and starting point for the quality assessment as well as life prediction of the product.