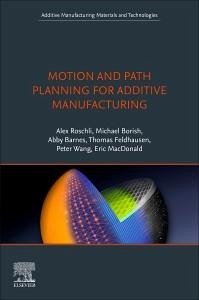
Motion and Path Planning for Additive Manufacturing
Versandkostenfrei!
Nicht lieferbar
Motion and Path Planning for Additive Manufacturing takes a deep dive into the concepts and computations behind slicing software - the software that uses 3D models to generate the commands required to control the motion of a 3D printer and ultimately construct objects. Starting with a brief review of the different types of motion in additive systems, this book walks through the steps of the path planning process and discusses the different types of toolpaths and their corresponding function in additive manufacturing. Planar, non-planar, and off-axis path planning are examined and explained. Th...
Motion and Path Planning for Additive Manufacturing takes a deep dive into the concepts and computations behind slicing software - the software that uses 3D models to generate the commands required to control the motion of a 3D printer and ultimately construct objects. Starting with a brief review of the different types of motion in additive systems, this book walks through the steps of the path planning process and discusses the different types of toolpaths and their corresponding function in additive manufacturing. Planar, non-planar, and off-axis path planning are examined and explained. This book also presents pathing considerations for different types of 3D-printers, including extrusion, non-extrusion, and hybrid systems as well as 3- and 5-axis systems. Engineers, researchers, and designers in the additive manufacturing field can use this book as a reference for every step of the path planning process, as well as a guide that explains the computations underlying the creation and use of toolpaths.