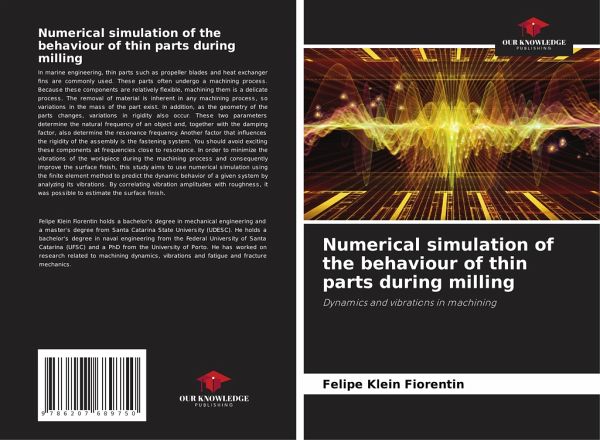
Numerical simulation of the behaviour of thin parts during milling
Dynamics and vibrations in machining
Versandkostenfrei!
Versandfertig in 6-10 Tagen
29,99 €
inkl. MwSt.
PAYBACK Punkte
15 °P sammeln!
In marine engineering, thin parts such as propeller blades and heat exchanger fins are commonly used. These parts often undergo a machining process. Because these components are relatively flexible, machining them is a delicate process. The removal of material is inherent in any machining process, so variations in the mass of the part exist. In addition, as the geometry of the parts changes, variations in rigidity also occur. These two parameters determine the natural frequency of an object and, together with the damping factor, also determine the resonance frequency. Another factor that influ...
In marine engineering, thin parts such as propeller blades and heat exchanger fins are commonly used. These parts often undergo a machining process. Because these components are relatively flexible, machining them is a delicate process. The removal of material is inherent in any machining process, so variations in the mass of the part exist. In addition, as the geometry of the parts changes, variations in rigidity also occur. These two parameters determine the natural frequency of an object and, together with the damping factor, also determine the resonance frequency. Another factor that influences the rigidity of the assembly is the fastening system. You should avoid exciting these components at frequencies close to resonance. In order to minimize the vibrations of the workpiece during the machining process and consequently improve the surface finish, this study aims to use numerical simulation using the finite element method to predict the dynamic behavior of a given system by analyzing its vibrations. By correlating vibration amplitudes with roughness, it was possible to estimate the surface finish.