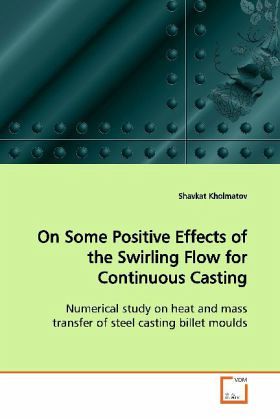
On Some Positive Effects of the Swirling Flow for Continuous Casting
Numerical study on heat and mass transfer of steel casting billet moulds
Versandkostenfrei!
Versandfertig in 6-10 Tagen
32,99 €
inkl. MwSt.
PAYBACK Punkte
16 °P sammeln!
Continuous caster mould is the last and importantstage in the steelmaking process where inclusionscan be either generated or removed. With increasingcasting speed using conventional immersion nozzlescritical problems, such as unstable bulk mould flow,have been noticed. Mould flux entrapment due tovortex and shearing action from the oscillatingsurface waves have become of particular concern. Itis, therefore, necessary to have a calm inlet flow atthe entrance of the mould.Recently, it has been acknowledged that a swirl bladeplaced at the upstream end of the nozzle effectivelyresolves these probl...
Continuous caster mould is the last and important
stage in the steelmaking process where inclusions
can be either generated or removed. With increasing
casting speed using conventional immersion nozzles
critical problems, such as unstable bulk mould flow,
have been noticed. Mould flux entrapment due to
vortex and shearing action from the oscillating
surface waves have become of particular concern. It
is, therefore, necessary to have a calm inlet flow at
the entrance of the mould.
Recently, it has been acknowledged that a swirl blade
placed at the upstream end of the nozzle effectively
resolves these problems. Therefore, to increase our
knowledge on swirling flow fundamental mathematical
models of a billet mould equipped with a swirl blade
in the nozzle have been developed. The model is used
to study the effects of changing nozzle tilt angle
and mould aspect ratio on heat and mass transfer in
the round and square moulds. Data from water model
experiments are used to verify the mathematical model
predictions. A fairly good agreement between physical
modeling data and predictions was found, which
ensured that the numerical models are reliable.
stage in the steelmaking process where inclusions
can be either generated or removed. With increasing
casting speed using conventional immersion nozzles
critical problems, such as unstable bulk mould flow,
have been noticed. Mould flux entrapment due to
vortex and shearing action from the oscillating
surface waves have become of particular concern. It
is, therefore, necessary to have a calm inlet flow at
the entrance of the mould.
Recently, it has been acknowledged that a swirl blade
placed at the upstream end of the nozzle effectively
resolves these problems. Therefore, to increase our
knowledge on swirling flow fundamental mathematical
models of a billet mould equipped with a swirl blade
in the nozzle have been developed. The model is used
to study the effects of changing nozzle tilt angle
and mould aspect ratio on heat and mass transfer in
the round and square moulds. Data from water model
experiments are used to verify the mathematical model
predictions. A fairly good agreement between physical
modeling data and predictions was found, which
ensured that the numerical models are reliable.