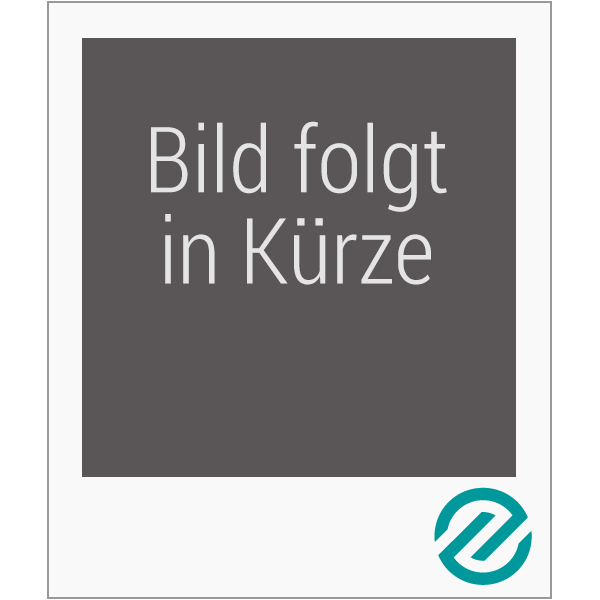
Optimizing Thermal Behavior of Compact Heat Exchanger
Thermal Behavior Analysis
Versandfertig in 6-10 Tagen
29,99 €
inkl. MwSt.
PAYBACK Punkte
15 °P sammeln!
One of the key aspects of industrial machines, devices, and processes is heat transfer to maintain their functionality and achievements for better product quality. Therefore, various types of heat exchangers are involved to remove heat and maintain desired operating temperatures. However, to determine the requirement of space the size of a heat exchanger is matters (i.e. dimensions) of the machine/device or plant treatment. The objective of this study is to design theoretically analyze, then optimize performance using CFD. The theoretical study using the LMTD method for concurrent heat exchang...
One of the key aspects of industrial machines, devices, and processes is heat transfer to maintain their functionality and achievements for better product quality. Therefore, various types of heat exchangers are involved to remove heat and maintain desired operating temperatures. However, to determine the requirement of space the size of a heat exchanger is matters (i.e. dimensions) of the machine/device or plant treatment. The objective of this study is to design theoretically analyze, then optimize performance using CFD. The theoretical study using the LMTD method for concurrent heat exchange is done, while the pressure drops and energy consumption are calculated using the Kern method. In this study, CFD ANAYALSIS THREE CASES analyzed the behavior of heat transfer, mass flow rates, pressure drops, flow rates, and eddies of tube bundle currents in the heat exchanger. The theoretically and CFD-based analysis is shown on only 1.15% in terms of hot fluid cooling performance. Overall, the results of this study confirm that CFD modeling can hold promise for heat exchanger design and optimization, allowing you to test many design options without building physical prototypes.