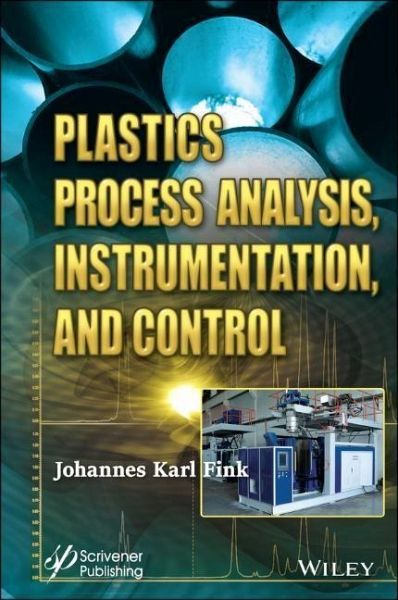
Plastics Process Analysis, Instrumentation, and Control
Versandkostenfrei!
Versandfertig in 2-4 Wochen
201,99 €
inkl. MwSt.
Weitere Ausgaben:
PAYBACK Punkte
101 °P sammeln!
This book focuses on plastics process analysis, instrumentation for modern manufacturing in the plastics industry.Process analysis is the starting point since plastics processing is different from processing of metals, ceramics, and other materials. Plastics materials show unique behavior in terms of heat transfer, fluid flow, viscoelastic behavior, and a dependence of the previous time, temperature and shear history which determines how the material responds during processing and its end use. Many of the manufacturing processes are continuous or cyclical in nature. The systems are flow system...
This book focuses on plastics process analysis, instrumentation for modern manufacturing in the plastics industry.
Process analysis is the starting point since plastics processing is different from processing of metals, ceramics, and other materials. Plastics materials show unique behavior in terms of heat transfer, fluid flow, viscoelastic behavior, and a dependence of the previous time, temperature and shear history which determines how the material responds during processing and its end use. Many of the manufacturing processes are continuous or cyclical in nature. The systems are flow systems in which the process variables, such as time, temperature, position, melt and hydraulic pressure, must be controlled to achieve a satisfactory product which is typically specified by critical dimensions and physical properties which vary with the processing conditions.
Instrumentation has to be selected so that it survives the harsh manufacturing environment of high pressures, temperatures and shear rates, and yet it has to have a fast response to measure the process dynamics. At many times the measurements have to be in a non-contact mode so as not to disturb the melt or the finished product. Plastics resins are reactive systems. The resins will degrade if the process conditions are not controlled. Analysis of the process allows one to strategize how to minimize degradation and optimize end-use properties.
Process analysis is the starting point since plastics processing is different from processing of metals, ceramics, and other materials. Plastics materials show unique behavior in terms of heat transfer, fluid flow, viscoelastic behavior, and a dependence of the previous time, temperature and shear history which determines how the material responds during processing and its end use. Many of the manufacturing processes are continuous or cyclical in nature. The systems are flow systems in which the process variables, such as time, temperature, position, melt and hydraulic pressure, must be controlled to achieve a satisfactory product which is typically specified by critical dimensions and physical properties which vary with the processing conditions.
Instrumentation has to be selected so that it survives the harsh manufacturing environment of high pressures, temperatures and shear rates, and yet it has to have a fast response to measure the process dynamics. At many times the measurements have to be in a non-contact mode so as not to disturb the melt or the finished product. Plastics resins are reactive systems. The resins will degrade if the process conditions are not controlled. Analysis of the process allows one to strategize how to minimize degradation and optimize end-use properties.