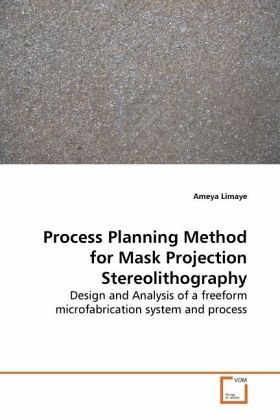
Process Planning Method for Mask Projection Stereolithography
Design and Analysis of a freeform microfabrication system and process
Versandkostenfrei!
Versandfertig in 6-10 Tagen
51,99 €
inkl. MwSt.
PAYBACK Punkte
26 °P sammeln!
Mask Projection Stereolithography is a high resolution manufacturing process that builds parts layer by layer in a photopolymer. A MPSLA system is designed and assembled. The irradiance incident on the resin surface when a given bitmap is imaged onto it is modeled as the Irradiance model. Print-through errors occur in multi-layered builds because of radiation penetrating beyond the intended thickness of a layer, causing unwanted curing. In this research, the print through errors are modeled in terms of the process parameters used to build a multi layered part. To this effect, the Transient lay...
Mask Projection Stereolithography is a high
resolution manufacturing process that builds parts
layer by layer in a photopolymer. A MPSLA system is
designed and assembled. The irradiance incident on
the resin surface when a given bitmap is imaged onto
it is modeled as the Irradiance model. Print-through
errors occur in multi-layered builds because of
radiation penetrating beyond the intended thickness
of a layer, causing unwanted curing. In this
research, the print through errors are modeled in
terms of the process parameters used to build a
multi layered part. To this effect, the Transient
layer cure model is formulated, that models the
curing of a layer as a transient phenomenon, in
which, the rate of radiation attenuation changes
continuously during exposure. The print through
model is used to formulate a process planning method
to cure multi-layered parts with accurate vertical
dimensions. The models formulated and validated in
this work are used to formulate a process planning
method to build MPSLA parts with constraints on
dimensions, surface finish and build time. The
process planning method is demonstrated by means of
a case study.
resolution manufacturing process that builds parts
layer by layer in a photopolymer. A MPSLA system is
designed and assembled. The irradiance incident on
the resin surface when a given bitmap is imaged onto
it is modeled as the Irradiance model. Print-through
errors occur in multi-layered builds because of
radiation penetrating beyond the intended thickness
of a layer, causing unwanted curing. In this
research, the print through errors are modeled in
terms of the process parameters used to build a
multi layered part. To this effect, the Transient
layer cure model is formulated, that models the
curing of a layer as a transient phenomenon, in
which, the rate of radiation attenuation changes
continuously during exposure. The print through
model is used to formulate a process planning method
to cure multi-layered parts with accurate vertical
dimensions. The models formulated and validated in
this work are used to formulate a process planning
method to build MPSLA parts with constraints on
dimensions, surface finish and build time. The
process planning method is demonstrated by means of
a case study.