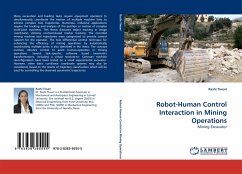
Robot-Human Control Interaction in Mining Operations
Mining Excavator
Versandkostenfrei!
Versandfertig in 6-10 Tagen
38,99 €
inkl. MwSt.
PAYBACK Punkte
19 °P sammeln!
Many excavation and loading tasks require equipment operators to simultaneously coordinate the motion of multiple machine links to achieve complex tool trajectories. Numerous industrial applications require the tracking and analysis of the position or motion of complex multi-joint machines. This thesis discusses object tracking in image coordinates utilizing contrast-based marker tracking. The recorded mining machine tool trajectories were categorized to provide control support for the operator. The new differential control technique for enhancing the efficiency of mining operations by automat...
Many excavation and loading tasks require equipment operators to simultaneously coordinate the motion of multiple machine links to achieve complex tool trajectories. Numerous industrial applications require the tracking and analysis of the position or motion of complex multi-joint machines. This thesis discusses object tracking in image coordinates utilizing contrast-based marker tracking. The recorded mining machine tool trajectories were categorized to provide control support for the operator. The new differential control technique for enhancing the efficiency of mining operations by automatically coordinating multiple joints is also described in the thesis. The concept involves robotics control to assist human-operators in mining operations. Several task-specific, software based kinematics transformations, including a virtual revolute-to- Cartesian machine reconfiguration have been tested on a small experimental excavator. However, other basic curvilinear coordinate systems may also be considered, based on the results of trajectory classification which will be used for controlling the observed parametric trajectories.