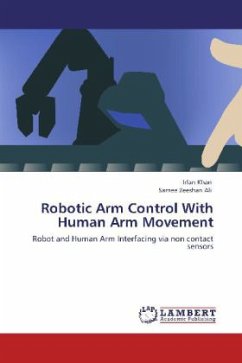
Robotic Arm Control With Human Arm Movement
Robot and Human Arm Interfacing via non contact sensors
Versandkostenfrei!
Versandfertig in 6-10 Tagen
32,99 €
inkl. MwSt.
PAYBACK Punkte
16 °P sammeln!
Digital technology and computers enabled the design of more flexible automation systems. Robots are becoming more and more flexible with progress in technology and programming techniques. The project is about controlling the industrial robotic arm via non-contact sensors. The project consists of three main parts; console box, control circuitry and robotic arm. Five PIC micro-controllers connected on an I2C network are used. Micro-controllers take the analog data from all sensors which are mounted on console box, convert it into digital form via built in ADC modules, process the data and conver...
Digital technology and computers enabled the design of more flexible automation systems. Robots are becoming more and more flexible with progress in technology and programming techniques. The project is about controlling the industrial robotic arm via non-contact sensors. The project consists of three main parts; console box, control circuitry and robotic arm. Five PIC micro-controllers connected on an I2C network are used. Micro-controllers take the analog data from all sensors which are mounted on console box, convert it into digital form via built in ADC modules, process the data and convert it into x, y, and z coordinates of the hand. After that it uses inverse kinematics equation to find out the parameters of motors on the robotic arm. Using angle/voltage transfer function a corresponding pulse width modulated signal is sent to the H-bridge circuits to control the motion of robotic arm.