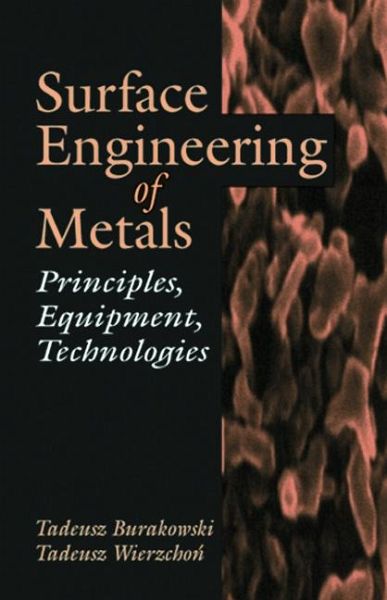
Surface Engineering of Metals
Principles, Equipment, Technologies
PAYBACK Punkte
145 °P sammeln!
Surface Engineering of Metals provides basic definitions of classical and modern surface treatments, addressing mechanisms of formation, microstructure, and properties of surface layers. Part I outlines the fundamentals of surface engineering, presents the history of its development, and proposes a two-category classification of surface layers. Discussions include the basic potential and usable properties of superficial layers and coatings, explaining their concept, interaction with other properties, and the significance of these properties for proper selection and functioning. Part II provide...
Surface Engineering of Metals provides basic definitions of classical and modern surface treatments, addressing mechanisms of formation, microstructure, and properties of surface layers. Part I outlines the fundamentals of surface engineering, presents the history of its development, and proposes a two-category classification of surface layers. Discussions include the basic potential and usable properties of superficial layers and coatings, explaining their concept, interaction with other properties, and the significance of these properties for proper selection and functioning. Part II provides an original classification of the production methods of surface layers. Discussions include the latest technologies in this field, characterized by directional or beam interaction of particles or of the heating medium with the treat surface.