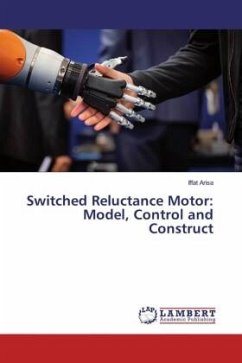
Switched Reluctance Motor: Model, Control and Construct
Versandkostenfrei!
Versandfertig in 6-10 Tagen
26,99 €
inkl. MwSt.
PAYBACK Punkte
13 °P sammeln!
The modelling and analysis of a switched reluctance motor is the initial task for the selection of the coupled mover. It must be able to achieve high speed and enough starting torque to actuate the coupled compressor and turbine, for the application of an automotive turbocharger. With the use of finite element analysis, a motor is designed to achieve the performance requirements of turbocharger coupling. The experiment is implemented that consist of an 800W 35,000 rpm switched reluctance motor coupled with a secondary switched reluctance motor and a heat gun to exemplify the turbine load. The ...
The modelling and analysis of a switched reluctance motor is the initial task for the selection of the coupled mover. It must be able to achieve high speed and enough starting torque to actuate the coupled compressor and turbine, for the application of an automotive turbocharger. With the use of finite element analysis, a motor is designed to achieve the performance requirements of turbocharger coupling. The experiment is implemented that consist of an 800W 35,000 rpm switched reluctance motor coupled with a secondary switched reluctance motor and a heat gun to exemplify the turbine load. The second major component is the controller and drive. Two controllers are selected for the experiment which consist of a general low cost solution and an optimized development board for prototyping optimization. The low cost control solution is implemented with an arduino uno and an assortment of relays configured into an asymmetrical half bridge.