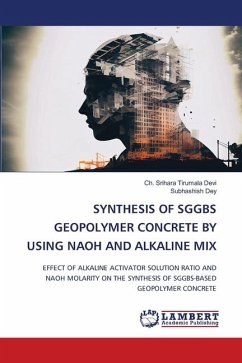
SYNTHESIS OF SGGBS GEOPOLYMER CONCRETE BY USING NAOH AND ALKALINE MIX
EFFECT OF ALKALINE ACTIVATOR SOLUTION RATIO AND NAOH MOLARITY ON THE SYNTHESIS OF SGGBS-BASED GEOPOLYMER CONCRETE
Versandkostenfrei!
Versandfertig in 6-10 Tagen
29,99 €
inkl. MwSt.
PAYBACK Punkte
15 °P sammeln!
Concrete is the second most material used in the world next to water. Ordinary Portland Cement (OPC) is used as primary binder to produce concrete. During manufacturing process of OPC, high emissions of greenhouse gases such as carbon dioxide (CO2) produced which results in polluting the surrounding environment. Geopolymer concrete reduces the cement usage and increases the usage of industrial by-products like fly ash, ground granulated blast furnace slag (GGBS), rice husk ash, silica fume in concrete. Geopolymer is a material resulting from the reaction of a source material that is rich in si...
Concrete is the second most material used in the world next to water. Ordinary Portland Cement (OPC) is used as primary binder to produce concrete. During manufacturing process of OPC, high emissions of greenhouse gases such as carbon dioxide (CO2) produced which results in polluting the surrounding environment. Geopolymer concrete reduces the cement usage and increases the usage of industrial by-products like fly ash, ground granulated blast furnace slag (GGBS), rice husk ash, silica fume in concrete. Geopolymer is a material resulting from the reaction of a source material that is rich in silica and alumina with alkaline solution. In this project cement is fully replaced with ground granulated blast furnace slag (GGBS), which is rich in silica and alumina. And alkaline activator solution used i.e., the combination of sodium hydroxide (NaOH) and sodium silicate (Na2Sio3) with ratios 1.5, 2, 2.5. And the variation of molarities like 10M, 12M, 14M of alkaline solution are taken. The compressive strength and split tensile strength of GGBS based geopolymer concrete for various mixes at ambient curing are compared.