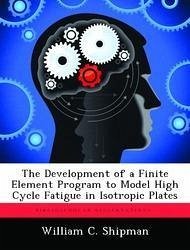
The Development of a Finite Element Program to Model High Cycle Fatigue in Isotropic Plates
Versandkostenfrei!
Versandfertig in über 4 Wochen
54,99 €
inkl. MwSt.
PAYBACK Punkte
27 °P sammeln!
As part of a joint AFRL-DAGSI turbine blade research effort, a computer program has been developed that uses a von Karman large-deflection two-dimensional finite element approximation to determine stress levels and patterns in isotropic thin plates. The dynamic loading of various plates has been carried out in order to model a high cycle fatigue situation. The research considered the various effects of mode shapes, resident frequency, non-linear cyclic effect, endurance limits, and stress variations within a high cycle fatigue environment. Two main initiatives were taken. First, a transient an...
As part of a joint AFRL-DAGSI turbine blade research effort, a computer program has been developed that uses a von Karman large-deflection two-dimensional finite element approximation to determine stress levels and patterns in isotropic thin plates. The dynamic loading of various plates has been carried out in order to model a high cycle fatigue situation. The research considered the various effects of mode shapes, resident frequency, non-linear cyclic effect, endurance limits, and stress variations within a high cycle fatigue environment. Two main initiatives were taken. First, a transient analysis tool was developed that calculates stress and displacement patterns over a period of time. This analysis also included the effects of damping. The second initiative developed a tool to calculate the eigenvalues (natural frequencies) and eigenvectors of a plate with a given geometry. The results indicated that it is possible to model fatigue at high frequencies using FE analysis and compare these findings with experimentation incorporating a shaker table. In this research, different geometries of plates were investigated to represent turbine blade configurations. One square plate and three trapezoidal plates were investigated. It was found that a linear relationship could be found between the loading amplitude and the resulting maximum stress. This relationship allows for the prediction of the needed loading amplitude to cause high cycle fatigue. It was also determined that by altering the geometry of the plate, the needed loading frequency or loading amplitude to reach a stress level that would initiate cracks could be minimized.