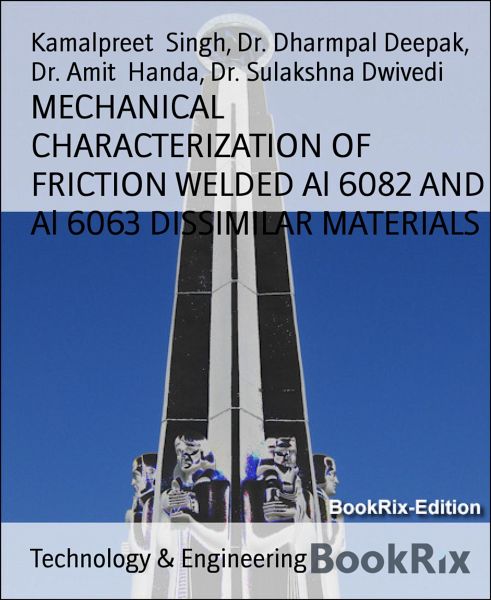
MECHANICAL CHARACTERIZATION OF FRICTION WELDED Al 6082 AND Al 6063 DISSIMILAR MATERIALS (eBook, ePUB)
FRICTION WELDING OF ALUMINIUM ALLOY
PAYBACK Punkte
0 °P sammeln!
Joining of dissimilar materials is one of the most essential needs of industries. There are various welding methods that have been developed to obtain suitable joints in various applications. However, friction welding is a solid state joining technique which utilizes the heat generated rubbing of two faying surfaces for the coalescence of the material. In the present study, an experimental setup was designed in order to achieve friction welding of plastically deformed Al 6082 and Al 6063 aluminium. Samples were welded under different burn off lengths and different rotational speeds. The tensil...
Joining of dissimilar materials is one of the most essential needs of industries. There are various welding methods that have been developed to obtain suitable joints in various applications. However, friction welding is a solid state joining technique which utilizes the heat generated rubbing of two faying surfaces for the coalescence of the material. In the present study, an experimental setup was designed in order to achieve friction welding of plastically deformed Al 6082 and Al 6063 aluminium. Samples were welded under different burn off lengths and different rotational speeds. The tensile strength, impact strength, Vickers micro hardness and SEM analysis of the welded joints were determined and evaluated on the results obtained from experimentations, the graphs were plotted. The experimental results indicate that burn off length and rotational speed has a significant effect on the mechanical properties of the joint and it is possible to increase the quality of the welded joint by selecting the optimum burn off lengths and rotational speeds.
Dieser Download kann aus rechtlichen Gründen nur mit Rechnungsadresse in A, B, CY, D, DK, EW, E, FIN, F, GR, IRL, I, L, M, NL, P, S, SLO, SK ausgeliefert werden.