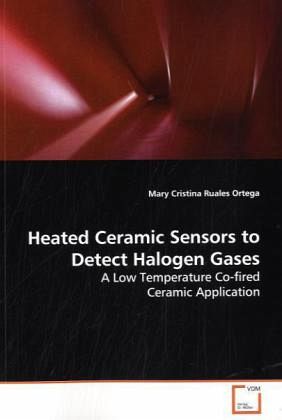
Heated Ceramic Sensors to Detect Halogen Gases
A Low Temperature Co-fired Ceramic Application
Versandkostenfrei!
Versandfertig in 6-10 Tagen
32,99 €
inkl. MwSt.
PAYBACK Punkte
16 °P sammeln!
The design, construction and optimization of a low power-high temperature heated ceramic sensor to detect leaking of halogen gases in refrigeration systems are presented. The manufacturing process was done with microelectronic assembly and the Low Temperature Co-fired Ceramic (LTCC) technology. Four basic sensor materials were fabricated and tested (Lithium Silicate, Sodium Silicate, Potassium Silicate, and Calcium Silicate). The evaluation of the sensor material, sensor size, operating temperature, bias voltage, electrodes size, firing temperature, gas flow, and sensor life was done. All sens...
The design, construction and optimization of a low
power-high temperature heated ceramic sensor to
detect leaking of halogen gases in refrigeration
systems are presented. The manufacturing process was
done with microelectronic assembly and the Low
Temperature Co-fired Ceramic (LTCC) technology. Four
basic sensor materials were fabricated and tested
(Lithium Silicate, Sodium Silicate, Potassium
Silicate, and Calcium Silicate). The evaluation of
the sensor material, sensor size, operating
temperature, bias voltage, electrodes size, firing
temperature, gas flow, and sensor life was done. All
sensors respond to the gas showing stability and
reproducibility. The sensors were analyzed, modeled
and the response to the gas was divided in surface
diffusion and bulk diffusion within the sensor. The
theoretical results obtained by the modeling of the
sensor were in agreement with the experimental
values.
power-high temperature heated ceramic sensor to
detect leaking of halogen gases in refrigeration
systems are presented. The manufacturing process was
done with microelectronic assembly and the Low
Temperature Co-fired Ceramic (LTCC) technology. Four
basic sensor materials were fabricated and tested
(Lithium Silicate, Sodium Silicate, Potassium
Silicate, and Calcium Silicate). The evaluation of
the sensor material, sensor size, operating
temperature, bias voltage, electrodes size, firing
temperature, gas flow, and sensor life was done. All
sensors respond to the gas showing stability and
reproducibility. The sensors were analyzed, modeled
and the response to the gas was divided in surface
diffusion and bulk diffusion within the sensor. The
theoretical results obtained by the modeling of the
sensor were in agreement with the experimental
values.